
Cutting fluids for CNC machining processes
A cutting fluid is a substance designed specifically for metal-working and machining processes where it acts as a coolant and lubricant. This fluid is applied while the machining is being done. Application methods for cutting fluids include flooding, fluid jetting, mist spraying, etc.

What is CNC cutting fluid and the Functions of Cutting Fluid During CNC Machining
CNC machining is a subtractive manufacturing technology where a cutting tool attached to a spinning spindle removes material from the workpiece, to accomplish the required machining operation.

The Significance of CAM Post Processors and the Most Popular Post Processors
Machine design and control are accomplished using CAD and CAM technologies. Machines require post-processors to make sure the code that is provided to them is readable and understandable and to maximize machine performance.
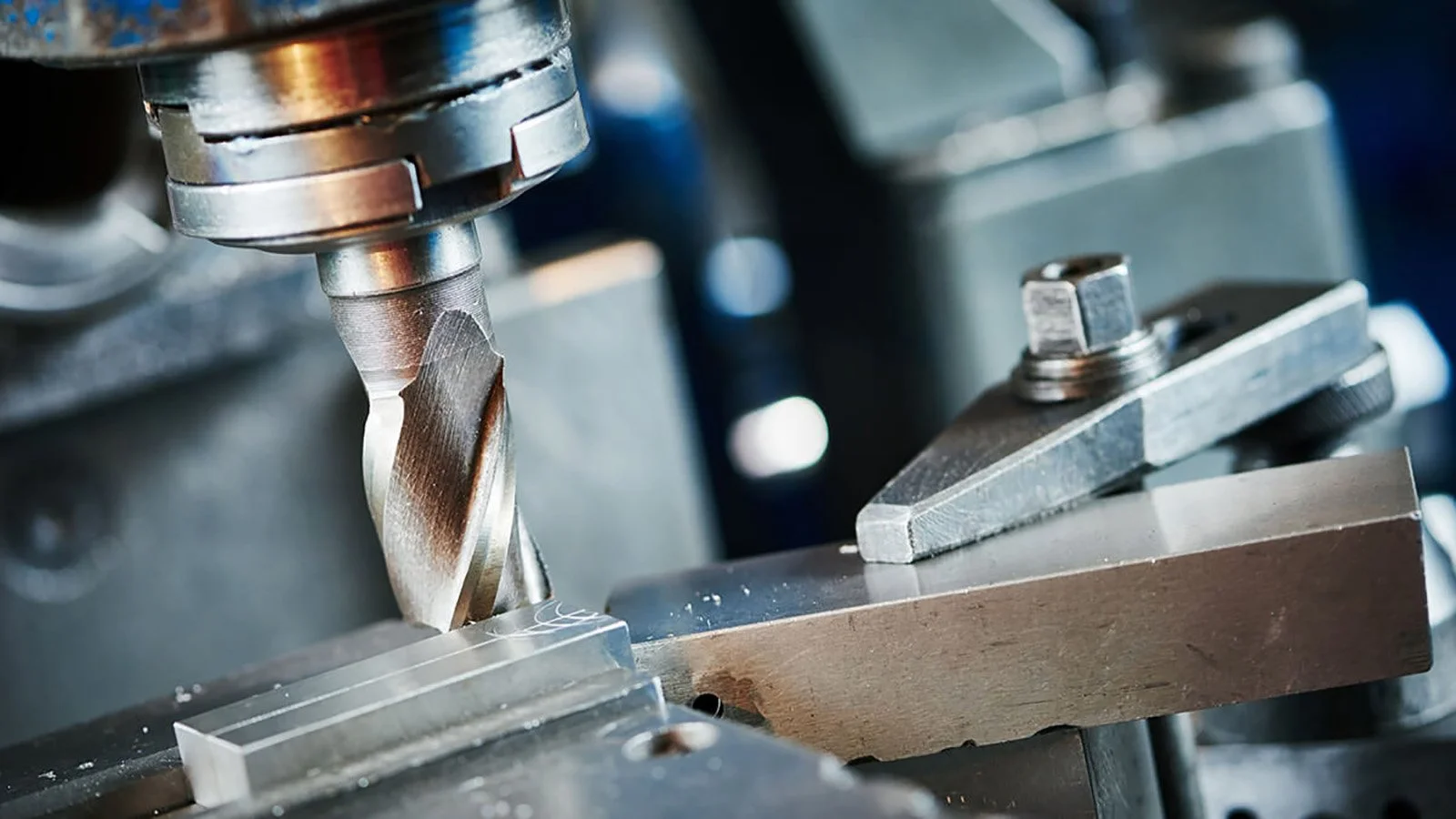
A Set of Pictures to Help You Understand the Common Methods of Machining
The key of turning is to rotate the workpieces to be processed, and then move the linearly moving tool close to them to carve the surface of the workpiece.
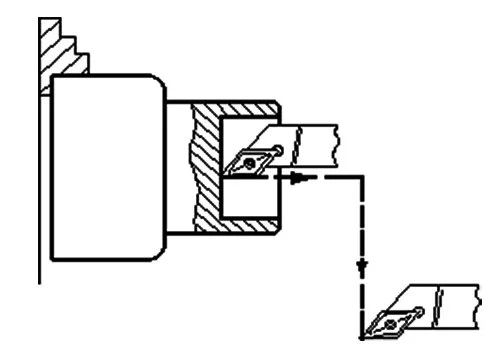
Three methods of retracting the turning tool of CNC lathe
In the process of CNC machine tool processing, in order to improve the processing efficiency, the tool moves from the starting point or tool change point to the position close to the workpiece and returns to the starting point or tool change point after processing in G00 (rapid point positioning) mode. The principle of considering the tool retraction route is: first, to ensure safety, that is, not to collide with the workpiece during the tool retraction process; second, to consider the shortest tool retraction route, shorten the empty stroke, and improve production efficiency.

Types and uses of CNC lathe tools
The turning tool is the most widely used single-edged tool, and it is also the basis for learning and analyzing various tools. Turning tools are used on various lathes to process outer circles, inner holes, end faces, threads, grooves, etc. According to the structure, turning tools can be divided into integral turning tools, welding turning tools, machine clamp turning tools, indexable turning tools, and forming turning tools. Among them, the application of indexable turning tools is becoming more and more extensive, and the proportion of turning tools is gradually increasing.
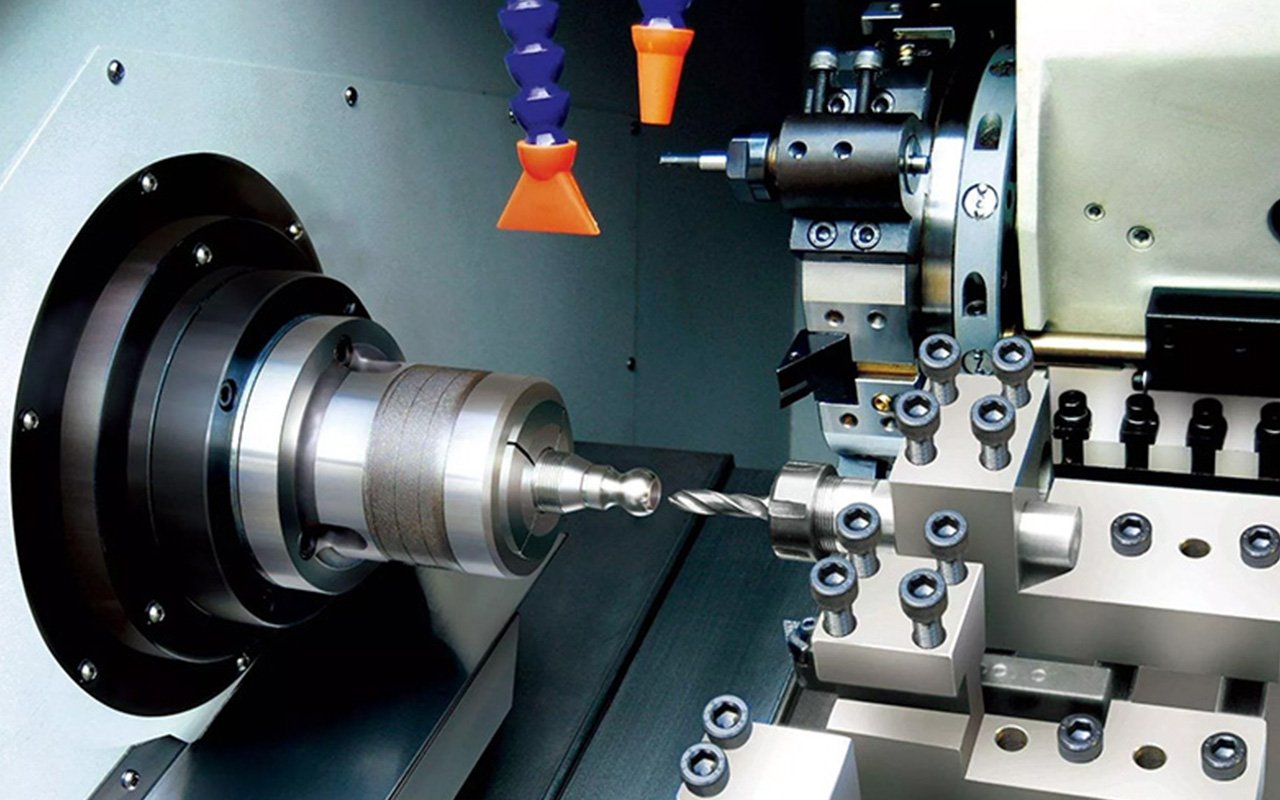
What is the difference between a CNC lathe and a CNC milling machine?
CNC lathes and CNC milling machines are both CNC machine tools. Both machine tools use programs to specify their tool paths. The following is the difference between the two in terms of working principles and uses.
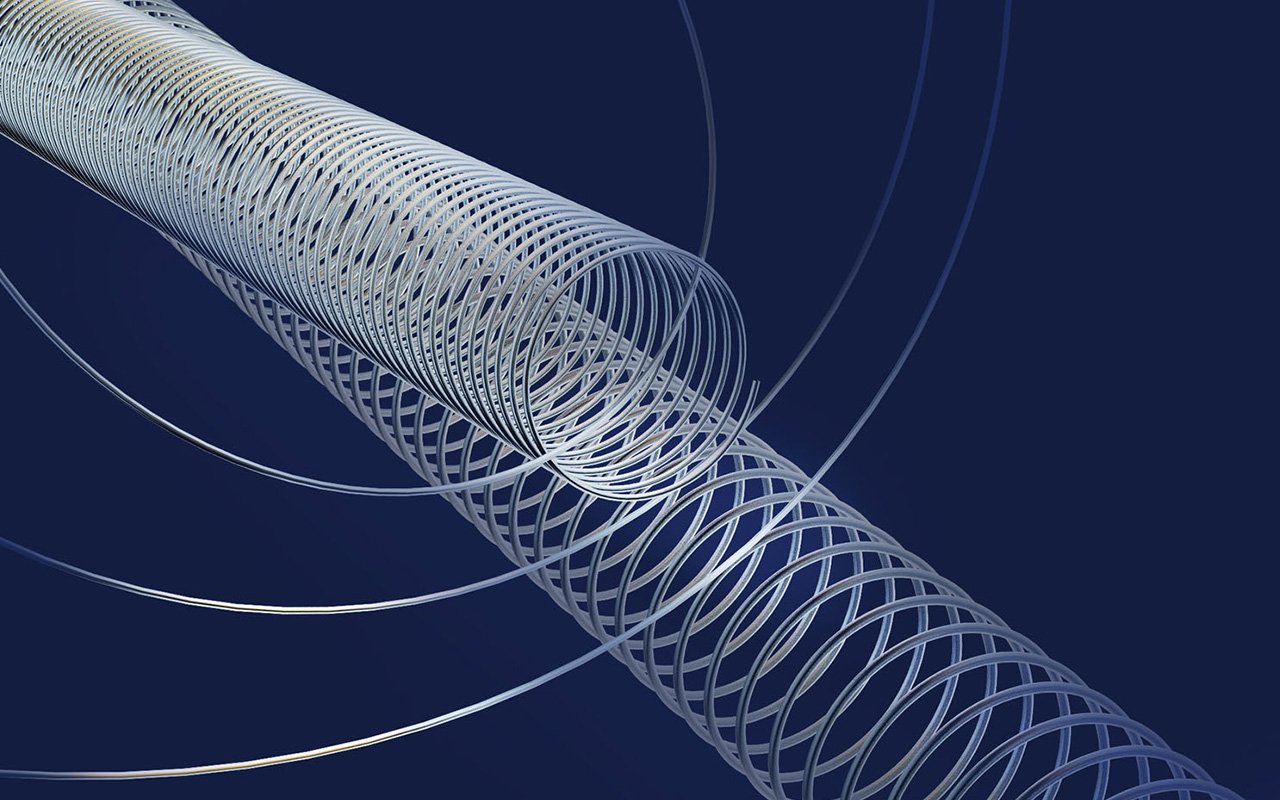
Three special functions of titanium
It refers to the ability of Ti-50%Ni (atomic) alloy to restore its original shape under certain temperature conditions. This material is called shape memory alloy.

Turning, milling, planing, grinding, drilling, boring, what kind of precision can be achieved
The workpiece rotates, and the turning tool moves in a straight line or a curved line in the plane. Turning is generally carried out on a lathe to process the inner and outer cylindrical surfaces, end surfaces, conical surfaces, forming surfaces, and threads of the workpiece.

These parts are really hard to measure. What should I do?
Standard measuring tools such as micrometers or calipers are commonly used "tools" for measuring flat and parallel features or inner/outer diameters of workpieces. However, when measuring workpieces with complex shapes, such as curved surfaces or narrow grooves, it may be difficult for standard universal measuring tools to reach the accurate measurement position. It is relatively easier and more economical to choose dedicated non-standard measuring tools.

How to Calculate CNC Speed and Feed
Each tool will adopt different processing parameters for different processing materials. In the field of milling, tool manufacturers develop more targeted coating technologies by optimizing tool materials to improve processing efficiency.
Through the combination of various elements in the material, we can see thousands of machinable raw materials. To process these materials, we must know the processing performance of this material, and also know the method that should be optimized for processing.

10 properties of titanium
Titanium is an element with an atomic number of 22 in the periodic table. It is a subgroup element of the fourth period, namely group IVB. In addition to titanium, this group of elements also includes zirconium and hafnium. Their common feature is that they have a high melting point and can be dissolved on their surface at room temperature. Form a stable oxide film.

In CNC milling, down milling or up milling?
In CNC machining, the rotation direction of the milling cutter generally remains unchanged, but the feed direction changes. There are two common phenomena in milling processing: down milling and up milling.
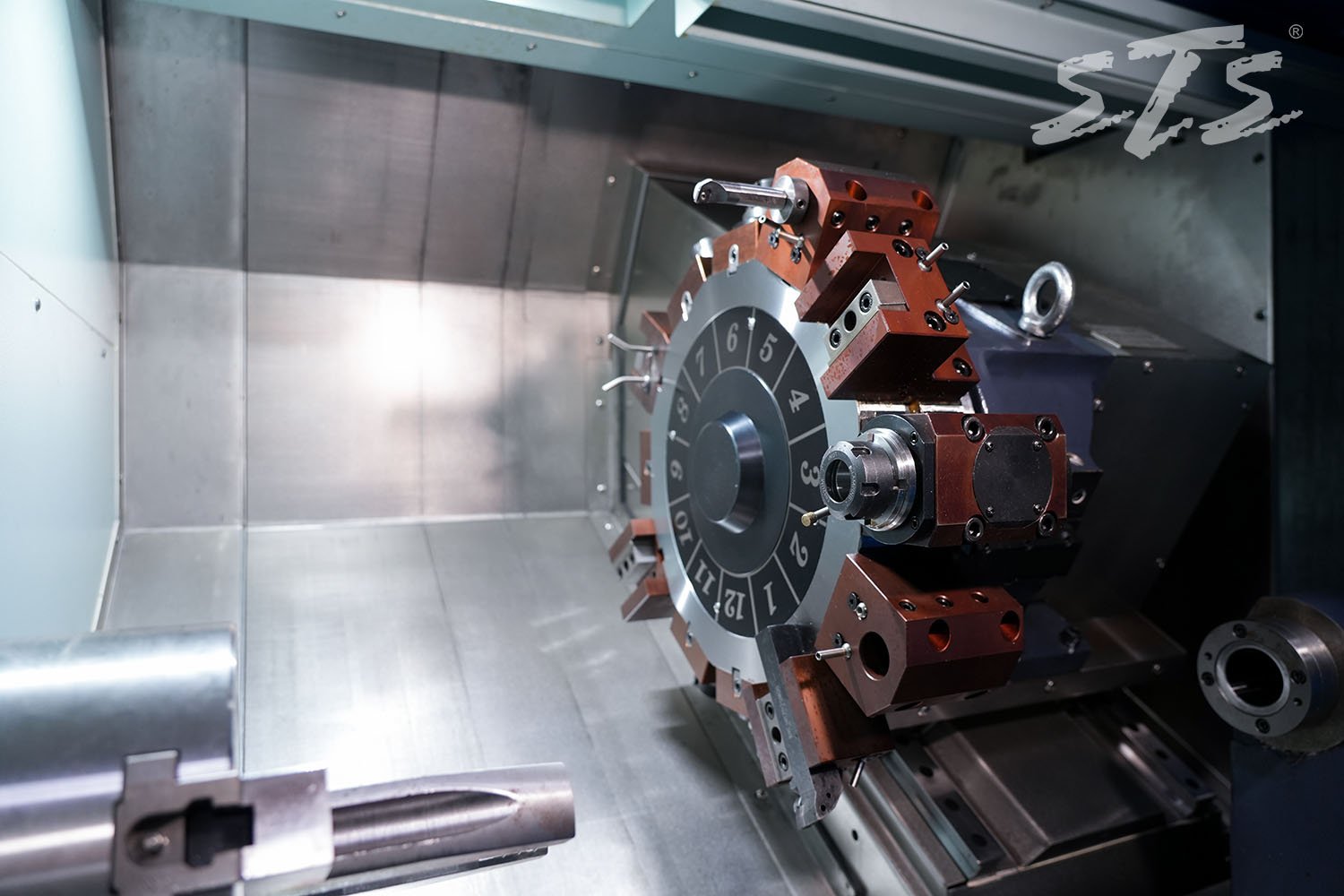
Wedge-Type Y-Axis CNC Lathe VS Real (True) Y-Axis CNC Lathe
Wedge-Type Y-Axis CNC Lathe: The wedge-type Y-axis mechanism utilizes a wedge block to position the tool off-center, enabling Y-axis movement. It allows for off-center drilling, milling, and other complex machining operations.
Real (True) Y-Axis CNC Lathe: A true Y-axis CNC lathe incorporates a dedicated Y-axis that enables vertical movement of the cutting tool perpendicular to the spindle axis. This provides precise control over the Y-axis movement and offers increased versatility in machining operations.
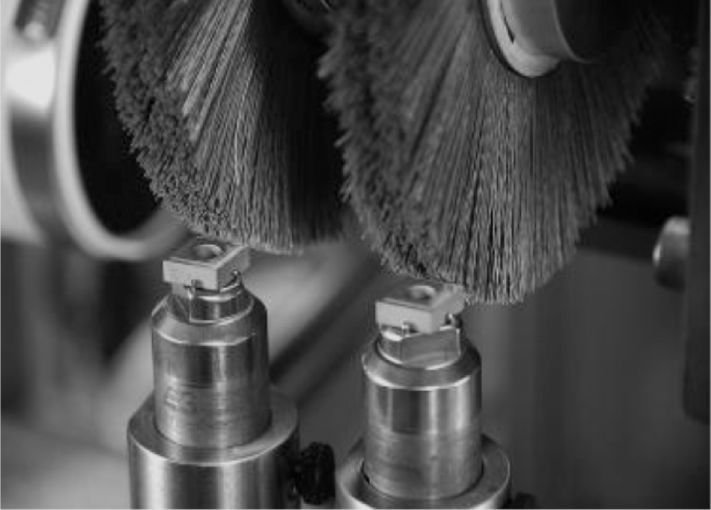
Why are tools deliberately "dulled"?
Isn’t the faster the CNC tools used in machining centers, the better? Why do they need to be passivated? In fact, tool passivation is not what everyone understands literally, but a way to increase the service life of tools. Improve tool quality through processes such as smoothing, polishing, and deburring. This is actually a normal process after the tool is finely ground and before coating.
What precision tolerance levels can be achieved for various machining processes?
We deal with machining every day. Do you know what precision tolerance levels can be achieved in turning, milling, planing, grinding, drilling and boring?
Tolerance level refers to the level that determines the degree of dimensional accuracy. The national standard stipulates that it is divided into 20 levels, from IT01, IT0, IT1, IT2 to IT18. The larger the number, the lower the tolerance level (processing accuracy), and the allowable variation range of size (tolerance The larger the value), the less difficult it is to process.
Product parts require different processing accuracy depending on their functions, and the selected processing forms and processing techniques are also different. This article introduces the machining accuracy that can be achieved by several common processing forms such as turning, milling, planing, grinding, drilling, and boring.

CNC lathe tool shape and usage
The types of turning tool tips generally used are as follows: Rough turning tools, Fine turning tools, Round nose turning tools, Threading tools, Boring turning tools, End face turning tools and Parting off tools.
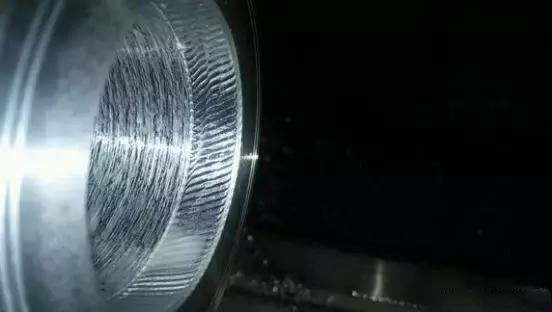
How to solve the problem of tool vibration in machining
When the force is applied, if the tool is not rigid enough, the tool body will deform, and a deviation will be produced in the direction of the force, and there will be a displacement. The tool has a displacement, so the depth of the knife will be smaller, the force will be smaller, and the displacement will be smaller. The generated displacement becomes smaller, and the tool moves in the opposite direction of the force, so that the cutting depth becomes larger, and the cutting becomes larger at the same time.
This is like comparing a tool to a long and thin wooden stick. One end is fixed and the other end is stressed, so the end away from the unfixed end will be deflected and rebound.
In this way, during the machining process, constantly changing cutting forces act on the tool and the workpiece, resulting in vibrations.
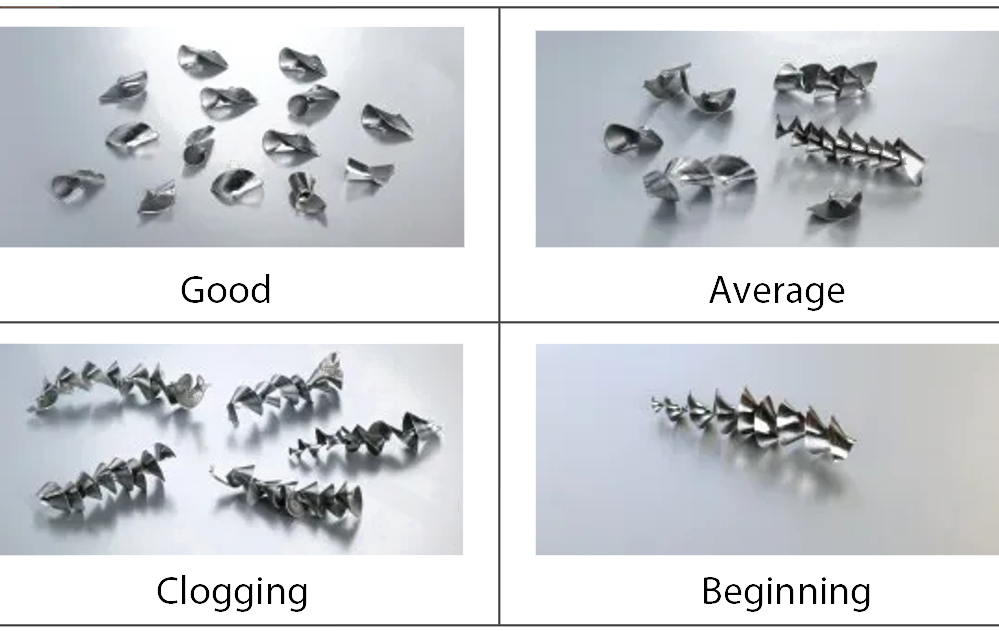
How to drill a perfect hole
Chip formation and chip evacuation are key issues in drilling and depend on workpiece material, choice of drill/insert geometry, coolant pressure/volume, cutting parameters.
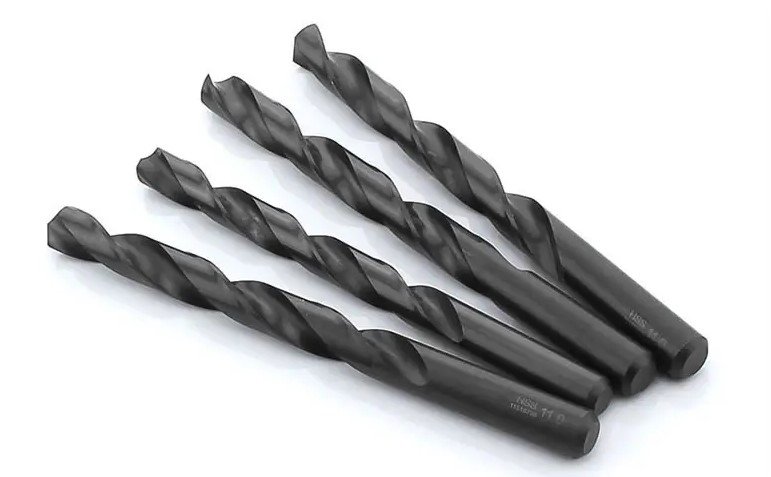
How to choose a drill bit for drilling?
Drilling processing, there are three basic conditions for selecting a drill bit: material, coating and geometric characteristics.